2. Biofuels Technologies
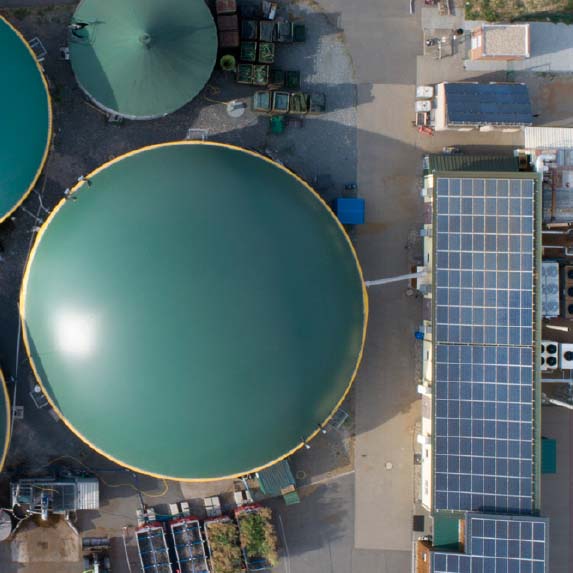
As energy from traditional fossil sources (oil, natural gas and coal) are progressively depleted and/or discouraged due to their impact on the overall GHG emissions, biomasses are more and more becoming a key asset for the production of sustainable fuels in the near future. The term biomass refers generically to the accumulation of a broad spectrum of animal and plant resources and their wastes. Although biomass carbon balance benefits from former plants’ utilization of CO2 for the photosynthetic processes, other factors should be taken into account like the water/nutrients consumption for cultivation, soil depletion and water/energy consumption during conversion. All these aspects will be addressed in the following sections of this chapter as well as in Chapter 3.
Traditionally, biomasses for biofuel production were identified exclusively with direct products from crops cultivation, mainly sugar and starchy crops or oil seeds. Biofuel obtained from these feedstocks are generally referred to as “first generation” (1G) biofuel. Although 1G feedstocks still make up the largest share for biofuel production, the exploitation of other feedstocks, such as agri-food residues and municipal/industrial wastes is gaining importance. This is the result of a significant effort to try to overcome the main issue of 1G biofuel, namely competition with food. Biofuels obtained from these non food-based sources are usually defined as “second generation” (2G) biofuels. Furthermore, algae feedstocks are attracting great attention due to their peculiar characteristics, mainly low land occupation, fast growth rate and availability of biomass. Given algae peculiar features and the relative novelty of their exploitation, biofuels obtained from such feedstock are qualified as “third generation” (3G).
Albeit fairly widespread, this classification is not the only one in the literature. Sometimes, a distinction is made according to the novelty of the process. As a result, bioethanol production from sugarcane (food-based) could be classified as 2G if novel industrial practice is applied. Equally, digestion of wastewaters would be considered 1G, although wastewaters are not food-based, because anaerobic digestion is an old, well-established process. Further criteria have been proposed, including also the properties of the fuel (i.e. profitability as drop-in biofuel). This broad range of definitions makes it even more challenging to make a clear comparison between the approaches to biofuel production.
For the sake of simplicity, we will stick to the former criteria of competition with food. Hence, production routes will be classified into two main groups, namely traditional and advanced technologies. The traditional group encompasses 1G biofuels from food-based feedstocks, that is to say bioethanol from sugar/starchy crops, biodiesel from vegetable oils and possibly biogas from agricultural crops. On the other hand, the advanced group includes 2G and 3G production routes exploiting respectively residues/wastes, such as bioethanol from lignocellulosic crops, thermochemical conversion of agri-food residues or digestion of manure, and algae (biodiesel, jet-fuel, biomethane, etc.). Such a scheme is quite common and it is very similar to the one reported in Figure 2.1. Primary biofuels, included in the figure, refer to untreated (at most pelletized), usually woody biomasses which are directly exploited for energy production. According to the specific focus of the report, only secondary biofuels will be taken into account in the following.
FIGURE 2.1 Classification of biofuels.[1]
As a final introductory remark, it is important to recall that biofuels usually display rather different composition and functional properties (density, viscosity, cloud point, etc.) compared to fossil fuels. This is especially true for 1G biofuels like bioethanol and biodiesel -- which still makes up the majority of global biofuel production -- but it also applies to many 2G/3G products. In fact, direct use of biofuels as a standalone feed for engines is usually not possible. Such issue can be overcome in two main ways. The first one is to design new engines capable of processing the raw biofuels coming from conversion of biomass. This is challenging from a technological standpoint, especially due to the high variability of feedstocks, but not unattainable. For instance, flex-vehicles are capable of processing different blends of gasoline and bioethanol up to 100% of biofuel. The other solution is upgrading of biofuels through additional treatments. The resulting biofuels, usually indicated as "drop-in", can thus operate with existing engines without major adjustment thanks to their superior properties.
2.1 Policies and targets for biofuels
Biofuel production at the industrial and commercial scale is relatively new compared to well-consolidated petroleum- derived fuels. Indeed, the lack of infrastructure and technological know-how in many developing countries qualify the biofuel production routes as infant and risky technology. Therefore, energy policies in such context are crucial for the fostering of biofuel platforms through the definition/standardization of the different bio-derived products and the unfolding of different supportive actions for their strengthening in the local and global market.
Policies arise according to different needs. Energy security is surely one of the most recurrent. In fact, the dependence on imported sources of energy, combined with price volatility and supply disruptions, make the availability of local energy sources very attractive. Secondly, the chance or need to promote economic and social quality of rural areas, especially in developing countries, can give an impulse to biofuel policies. Such contributions may come in many forms and may affect biofuel technologies at different levels along the supply chain. For instance, subsidies in the agri-food sectors, tariffs and tax incentives as well as subsidies for biofuels or flex-fuel vehicles purchase are pretty common. Moreover, a common policy adopted in OECD states is the definition of mandatory levels of blending of biofuels in conventional liquid fuels, acting as a trigger for biofuel industry growth.
European Union has put in motion a set of supporting actions during the last decades within the member states. Three fundamental Directives (EU) on biofuel legislation were approved in 2003 (2003/30/EC, 2003/96/EC and 2003/17/EC), setting the stage for national initiatives via voluntary targets for biofuel consumption and biofuel share in the energy balance as well as the application of tax incentives for biofuels. At the same time, support to the biofuel market came also from the Common Agricultural Policy and Rural Development Policy. More recently, Directive (EU) 2018/2001 (promotion of the use of energy from renewable sources) was approved by European Parliament in December 2018, defining the new target of 32% share of energy from renewable sources in gross final consumption of energy by 2030. Additionally, the directive requires each member state to compel fuel suppliers with obligations so that the share of renewable energy within the final consumption of energy in the transport sector is at least 14% by 2030.
Similarly, the United States deployed a set of tax incentives for biofuel production in 2005 with the Energy Policy Act. The Act also established some quantitative targets in the form of Renewable Fuels Standard (RFS) program. Later, the Energy Independence and Security Act of 2007 defined new, more demanding targets, namely a phased increase of biofuels volume up to 36 billion gallons by 2022, mainly covered by advanced biofuels. In addition, the Biomass Crop Assistance and Biorefinery Assistance Programs are supplementary tools for sustaining biofuels deployment through assistance to landowners and operators involved in biofuel feedstocks production as well as funding of newly constructed and retrofitted plants for advanced biofuel production.
2.2 Traditional biofuels
This section deals with 1G biofuel technologies, namely fermentation of sugar or starchy crops to bioethanol, transesterification of vegetable oils (FAME), hydrogenated vegetable oils (HVO) and anaerobic digestion of agricultural crops to biogas. These technologies easily encompass the vast majority of the current biofuel production (more than 90%). In fact, it was estimated that conventional ethanol and biodiesel/HVO accounted respectively for 71% and 20% of 2018 biofuel production (154.4 billion L).[2] This dominance of traditional technologies is the result of a variety of factors, but one of the most prominent surely is the high risks connected to the deployment of many advanced biofuel technologies.
By contrast, traditional technologies are well-consolidated and the chemistry of the process is typically well- understood, thus lowering installation and operating costs and, in general, the risks of investing in commercial- scale plants. However, such processes essentially rely on food-based feedstocks, such as sugar/starchy crops for bioethanol or vegetable oils for biodiesel/HVO. This brings up a number of issues. The yield of biofuel per area of land occupied is typically low. Still, the main drawback is the reduction of available land for agriculture, arising competition with the food sector. Several approaches can be implemented to overcome this shortcoming. For instance, crop rotation and integration with food cultivation is possible. Also, optimization of farming and harvesting processes can significantly improve the yield per area of land, that is to say to reduce the required land with equal fuel productivity. Finally, selected crops able to grow well on non-arable soils may allow mobilizing new land, although biodiversity, soil balance and pre-existing uses of marginal lands should be safeguarded as well.
2.2.1 Bioethanol from sugar and starchy crops
Bioethanol is obtained from the biochemical conversion of agricultural crops through yeasts fermentation. It is a very old, well-established technology and it currently makes up the largest share of biofuel production. In 2019 bioethanol capacity reached globally 115 billion L. In the United States, ethanol production reached 59.5 billion L in 2019[3], making it the first bioethanol producer globally with 52%. A similar level was expected for 2020, but the pandemic severely affected the ethanol industry and a 12% drop (the lowest output since 2014) is expected for the following year.[4] Brazil was the runner-up in 2019, with a bioethanol production of 36 billion L (31%). Brazil has also suffered strongly in 2020 due to gasoline demand drop, low oil prices and increased profitability of sugar cane on the sweeteners market. All these factors contributed to an expected fall of 16.5%.[5]
Sugar crops are the traditional feedstock for bioethanol production. This includes a sound variety of plants such as sugar cane, sugar beet, sugar millet and sweet sorghum, their main feature being the high content in fermentable sugars (sucrose, glucose and fructose). Preferred feedstocks are generally C4 plants -- they exploit a more efficient carbon fixation process (i.e. conversion of CO2 into organic compounds) compared to C3 plants.
Sugar cane is a perennial C4 grass with 12-24% of sugars on a wet weight basis, mainly sucrose (90%) with minor share of other sugars. Sugar cane is currently the largest feedstock for bioethanol production in Brazil, the second ethanol producer globally. In the EU, sugar beet is exploited alongside corn (see below) for 1G ethanol production. It contains 14-21% of fermentable sugars.[6] Sweet sorghum is another common feedstock, with high yield of both lignocellulosic fractions and fermentable sugars[7], making it eligible for both 1G bioethanol and lignocellulosic ethanol (see corresponding section in Advanced Technologies) production. Moreover, sweet sorghum contributes in small measure to the sugar market, contrarily to other crops like sugar cane and sugar beet.
Sugar crops are firstly milled and pressed to extract the sugar juice before fermentation. In the case of sugar cane, the extraction efficiency through pressing is very high (easily above 90%) and the main by-product is sugar cane bagasse (solid residues from pressing), which can be valorized again through conversion to lignocellulosic ethanol (see corresponding section in Advanced Technologies). Depending on the process, fermentation may be performed directly on the fresh juice or on a concentrated juice (thick juice). Fermentation is also applicable to molasses, the main by-product from sugar-refining, which still contains 45 to 60% sucrose and 5 to 20 % glucose and fructose.[8]
The other common feedstock for 1G ethanol is a vast group of starch-containing crops, including corn, wheat, barley, rye, sorghum, and cassava. corn is by far the most common feedstock for ethanol production in the US, the largest bioethanol producer. The starch content in the corn kernel is very high, easily above 70%, while simple sugars are only present in a few percent. On the other hand, wheat is the main crop used in Europe for ethanol. Given the relevance of these feedstocks, it is common in the literature to refer to them generically as corn crops to indicate either corn in the US or wheat in Europe. Barley and sorghum have a starch content of 50-75%, depending on the varieties, and can be exploited as rotation crops for corn. Sweet potatoes have also been considered recently as a possible feedstock due to their high starch content of 75%.
Starch is a polymeric carbohydrate made up by numerous glucose units and it is not a ready fermentable sugar. Thus, additional pre-treatment is required to reduce starch to simpler sugars (mainly glucose). This is achieved through hydrolysis and saccharification of the biomass by addition of proper enzymes (i.e. amylase). Depending on the process, the whole crops may be fed to the fermenter after grounding and hydrolysis (dry milling) or fractionation of the feedstock may be performed before hydrolysis/saccharification (wet milling). In the wet milling scheme, corn oil and gluten are recovered and they can be valorized as side-products, but the additional units result in increased capital costs and occupied area. Thus, the choice of process scheme should take into account the specific regional constraints on market and logistics of side-products.
Sugar or starchy biomass is then subjected to alcoholic fermentation. The biochemical reactions proceed anaerobically in presence of selected yeast strains (i.e. Saccharomyces cerevisiae) at controlled temperature of 30-35°C, allowing the conversion of fermentable sugars into ethanol and carbon dioxide. The stoichiometry of the reaction for glucose would suggest a high yield in ethanol. However, ethanol has an inhibitory effect on the yeasts, which progressively hamper the biomass growth. This results in limited conversion of sugars and especially low concentration of ethanol in the outlet solution, which typically accounts for 10% in volume at most. By exploiting alternative/engineered strains, it may be possible to raise the content up to 20% v/v. Thus, the outlet stream requires extensive concentration to reach 99% purity. This is achieved through a combination of evaporation, distillation columns and a final dehydration step to overcome the 95/5 azeotrope of the ethanol/water solution. In the case of corn feedstocks, distiller's dried grains and solubles (DDGS) are obtained as by-products. This is a mix of soluble organic and inorganic compounds which can either be sold as fodder, be used as substrate for anaerobic digestion to biomethane (see corresponding section in this chapter) or for energy integration in the process.
Clearly, production of CO2 negatively affects the carbon balance of the process. A possible solution is the integration of a carbon capture system, so that CO2 is directly recovered at the outlet of the fermenter. The recovered CO2 may be sold to local industries (i.e. beverages and food, enhanced oil recovery) or it may be injected for dedicated geologic carbon storage. The first option would raise the economic profitability of the plant, provided that the logistics is favorable and transportation costs are not too high, but has little impact on the overall carbon balance. Conversely, geologic carbon storage is probably the only option providing carbon negative use of CO2, but the technology costs are not always lower than the social cost of carbon, which may hinder its deployment. In any case, the highest costs for the process are tied to the purification (i.e. rectification plus dehydration) of ethanol, which is an energy- and water-intensive process. In particular, the dehydration step - required to achieve 99.5% purity of ethanol - is critical and may limit the economic profitability of the plant. Traditionally membrane or entrained distillation were the most common technologies for this stage, but many plants in the US and the EU also apply molecular sieves with pressure swing operation, providing energy savings for the process.[9]
Table 2.1 reports some average figures about three relevant feedstocks (sugarcane, corn and sugar beet). Although corn clearly stands out for ethanol conversion efficiency compared to sugar crops, it is also penalized by low biomass productivity. Sugar cane displays the highest yield thanks to the high biomass productivity.
Moreover, it is estimated that the average production cost of bioethanol in the US is 0.51-0.58 USD per liter of gasoline equivalent (lge), with a break-even of 64-76 USD per barrel.42 Hence, US bioethanol is not competitive with its fossil counterparts in domestic production, although policies support may play a relevant role in this respect. On the other hand, the production cost for Brazil bioethanol is estimated as 0.54-0.62 USD/lge, with a corresponding break-even of 50-60 USD per barrel,[10] making the biofuel competitive with domestic gasoline production.
TABLE 2.1. Biomass productivity (as tons of dry solids per hectare), ethanol conversion and ethanol yield for some relevant feedstocks. (Sugarcane[11], Corn[12][13][14][15], Sugar beet[16][17][18])
The obtained ethanol is generally used for blending with gasoline, according to quality standard ASTM D5798. The most common blending is E10 (10% of ethanol), but blending in the range 10.5-15% (E15) is also possible. Blending containing 50-85% of ethanol can be commercialized for use in flexible-fuel vehicles, which are designed to work properly with either gasoline, bioethanol or blending of variable amounts. Alternatively, the alcohol-to-jet process can be exploited to convert ethanol to drop-in jet fuel. In this process, ethanol is dehydrated and oligomerized (i.e. rearranged) into various hydrocarbons suitable for jet-fuel. The process was approved in 2016 according to ASTM D7566.
2.2.2 Biodiesel from vegetable oils (FAME)
Biodiesel is the conventional expression to refer to a mixture of fatty acid methyl esters (FAME), using vegetable oils and animal fats as feedstocks. In the last years, its production has constantly increased, as it is currently the only viable alternative for diesel engines for heavy-duty transport. For instance, US biodiesel production increased from 343 million gal in 2010 to 1.278 billion gal in 2014, an increase of 272% during this 5-year period.[19] In 2019, biodiesel and HVO (see following section) production reached 48 billion L and a slight contraction of 5% is expected for 2020 due to pandemic crisis.[20] European Union is still the largest producer with a biodiesel and HVO output of 15.7 billion L in 2019. In second place the United States reported 8.4 billion L for the same year.[21] The production decline in 2020 is expected to be small for both countries as the demand for biodiesel did not drop as much as for gasoline.
Vegetable oils (VO), both edible and non-edible, are the typical feedstock for biodiesel production, while animal fats and recycled frying oils account for a minor share. The most common cultivations include rapeseed, soybean, and oil palm, but feedstock distribution is highly localized. Rapeseed is the most common feedstock in the EU and displays an oil content around 40% of dry weight. Soybean is the typical choice in the US and in Brazil, which are also the largest producer worldwide with capacities of more than 100 million metric tons in 2018/2019.[22] Compared to rapeseed, soybean has a lower content in oil (about 20%), but it provides Nitrogen to the soil and can thus be easily integrated in crop rotation systems with Nitrogen-intensive crops, like corn in the US. Instead, oil palms require tropical or subtropical environments and are very widespread in Malaysia and Indonesia. The oil content usually falls in the range 45-55%.
Vegetable oils are extracted from the crops either through mechanical pressing or solvent extraction, usually using hexane as an extracting agent. Mechanical extraction efficiency varies in the range 60-80% depending on the selected press.[23] Conversely, solvent extraction can easily reach 95-99% efficiency and it yields a purer oil compared to pressing, but regeneration of the solvent through distillation is required, making it an energy- intensive process.[24] The obtained crude oil is then refined to remove phosphorus compounds (degumming with citric/phosphoric acid) and free fatty acids (neutralization with KOH/NaOH), the latter precipitating as soap stocks.
In principle, the refined VO could be used directly as fuel for biodiesel engines, thus cutting down the production flow solely to the extraction and refining of the oils. However, the higher viscosity and lower volatility of VO compared to diesel as well as reactivity of fatty acids may result in several issues, including clogging of filters/ injectors and build-up of deposits. Thus, conversion to fatty acids methyl esters (FAME) is preferred to the direct use of VO in diesel engines. VO are subjected to a catalyzed transesterification reaction in presence of methanol and a proper catalyst (e.g. methylates/hydroxides). The process is generally operated in the range 50-150°C for 30-180 min and it is exothermic (i.e. it releases energy during conversion). By properly tuning the operating conditions, yield in FAME can easily reach 90-95% and even higher values.[25] The main products are fatty acids methyl esters, which mainly differ from VO for their increased cetane number and reduced corrosivity. Along with FAME, glycerin is obtained as a by-product and is easily separated from the esters through gravity. It can be valorized for use in many industry sectors, such as thickening agents in cosmetics, food and paper. However, high level of purification is required, so that the economic profitability may vary greatly depending on the local market.
Owing to the wide variety of feedstocks, the resulting characteristics can vary substantially. Table 2.2 reports some estimates of oil productivity and biodiesel properties for different feedstocks. Palm oil stands out for oil productivity compared either to rapeseed or soybean. Also, it provides the highest cetane number, bearing in mind that average #2 Diesel display cetane number of around 50. However, the cloud point (i.e. behavior of the fuel at low temperature) is also a key parameter, as it strongly affects biodiesel application in colder climates and especially for aviation. This is particularly relevant considering the great difficulty in implementing electrification in the air transport segment. In this respect, rapeseed oils provide biodiesel with a lower cloud point compared to the other feedstocks, which makes it also viable for colder climates. Still further upgrading for use in aviation sector is needed, considering that winter Diesels provide a cloud point between -30 and -20 °C. On the other hand, palm oil use may be restricted to low fraction in blending due to its high cloud point (i.e. poor behavior at low temperature).
TABLE 2.2. Oil productivity, cetane number and cloud point according to different feedstocks. (Rapeseed[26][27][28], Soybean[29][30][31], Palm oil[32][33][34])
Table 2.3 reports volume potential and estimations of biodiesel production cost for 10 different countries, as retrieved by Johnston and Holloway (2007). The variation in costs between countries is strongly affected by feedstock price, as the cost of raw oil may account for 60--80% of the total price of biodiesel production.[35] More recently, IEA reported average production cost of biodiesel for US and Brazil of respectively 0.76-0.86 and 0.73-0.98 USD per liter of diesel equivalent (lde), which corresponds to break-even of 104-120 and 81-120 USD per barrel.[36] Thus, the cost of biodiesel was not competitive with fossil counterparts in either country, which was mainly due to soybean oil costs being almost three times higher than average crude oil prices in the same year. Moreover, the cost of biodiesel in both countries was generally higher than for ethanol.[37]
TABLE 2.3. Volume potential and production cost of biodiesel for 10 selected countries.[38]
Biodiesel can either be used directly as a fuel for diesel engines or it can be blended with fossil fuels before end- use, according to quality standards EN 14214 and ASTM D6751. A blending up to 20% by volume (B20) is generally considered an acceptable compromise for proper functioning of the engine without significant modification and similar performance compared to fossil fuel. Conversely, pure biodiesel usage (B100) should account for the lower energy content per unit volume compared to fossil diesel. Moreover, biodiesel may dissolve residues from fossil fuels deposited inside the engine, which are released causing clogging issues. Biodiesel was also reported to increase NOx emissions, but other pollutants emissions were decreased instead. In fact, an assessment of North American heavy-duty engine emissions from common biodiesel blend (B20) highlighted a reduction of particulate matter, hydrocarbons, and carbon monoxide by 10-20% compared to emissions from fossil diesel.[39]
2.2.3 Hydrotreating of vegetable oils (HVO/HEFA)
Hydrotreating is an alternative process to FAME, exploiting essentially the same feedstocks as transesterification (vegetable oils and/or animal fats). Oils and fats are subjected to catalytic saturation of double bonds and oxygen removal. The hydrotreating output is a mix of linear alkanes, usually referred to as hydroprocessed esters and fatty acids (HEFA). If plant oils are exploited as feedstock, the obtained biofuel is commonly indicated as hydrogenated vegetable oils (HVO). HEFA/HVO display some significant advantages compared to FAME, namely improved stability and low temperature behavior, making it a worthy candidate not only for biodiesel application, but also as a jet-fuel for aviation.
The process is conducted at high pressure (50-150 bar) and temperature in the range 300-450 °C and it is an exothermic process (i.e. energy is released during reaction). VO are converted to straight-chain alkanes and propane, while CO2 and water are obtained as side-products. The main process of saturation is often coupled with hydrocracking and isomerization (i.e. breaking and rearrangement of hydrocarbons chains), further boosting low temperature behavior of HVO, so that the resulting biofuel is often referred to as "iso-HVO". The yield is generally in the range 60-80%[40], but it can approach or even surpass 90% by proper selection of catalyst and operating conditions.[41] The obtained HEFA/HVO display lower viscosity compared to both diesel and biodiesel, cloud point between -10 and -30°C and high cetane number in the range 85-100 -- in fact, HEFA/HVO are also known as "super cetane" for this reason.[42] The main side-product is propane, which is more valuable compared to FAME glycerin.
The layout and operating conditions of biomass hydrotreating do not differ significantly from those employed in the petroleum industry for diesel/jet-fuel cuts. This is a great advantage compared to other biofuel technologies as it significantly lowers the risk connected to the process deployment. Moreover, revamping of decommissioned plants as well as VO hydroprocessing in the same reactor with fossil cuts (co-feeding) are possible with minor adjustments, easing integration and transition to bio-based production. Clearly, care must be taken in the possible presence of inhibitors/poisons for the catalyst, as the composition of biomasses is significantly different from the fossil feed to the hydrotreater.
Notable examples of HVO production are already available at the commercial scale, such as Neste in Rotterdam and Singapore (1.28 billion liters per year each), World Energy in California (150 million liters per year) and Diamond Green Diesel in Louisiana (1.04 billion liters per year). ENI plant in Venice (Italy) is the first case of repurposing of a disused refinery plant for the production of HVO. The facility ensures a yearly production of 462 million liters of HVO from vegetable oils, exploiting a patented hydrotreating technology known as Ecofining™ (ENI/UOP).[43] Other notable cases of reconversion of former refineries to hydro-processing of bio-oils are Total La Mede (France) (Total SA) and Marathon Petroleum Corp.[44]
According to IEA, HVO represents the only route to date that has been able to deliver commercially meaningful amounts of drop-in biofuels and these feedstocks are the main source of the bio-jet fuels that are currently used in aviation.[45] This is especially true considering that electrification of the aviation segment will require significant effort and time. Additionally, HVO can be also blended with diesel in different amounts, usually 30-50% v/v.
It is worth noticing that the addition of HVO is not reducing the fuel performances, but the other way around, and that HVO can also be exploited directly as a drop-in biofuel (according to quality standard EN 15940). These superior characteristics of HVO are boosting its market share. In 2018 the overall HVO production was 5.5 billion L, but it is expected to more than double in 2024, reaching almost 13 billion L.[46]
As for FAME, the main cost for HEFA/HVO production is still the feedstock price, which accounts for 60--75% of the final product cost.[47] In addition, hydrogen supply is required for the treatment. This is not an issue when performing co-feeding, as hydrogen is available in refineries from catalytic reforming. However, this is not the case for revamped or fully bio-based plants. Different approaches are available in this case for hydrogen supply. It could be produced directly from a minor share of the feedstock, but this is usually not very beneficial considering that the hydrogen amount in biomass is very limited (always less than 10%). Alternatively, green hydrogen from electrochemical split of water is possible, if access to a viable water source is available. The strategy for hydrogen supply will strongly depend on local constraints in terms of hydrogen price and water/feedstock availability. As a consequence, profitability of HVO processes will also be related to regional context. As a general rule, though, HVO may have lower production costs (especially in terms of capital investments) compared to FAME for the same feedstock.[48]
2.2.4 Crops digestion to biogas
When proper conditions are provided, agricultural crops can be broken down by microorganisms and converted to a gaseous mix of methane, CO2, and minor impurities. Such biochemical conversion, known as digestion, occurs naturally in anaerobic conditions (i.e. without oxygen) and it has long been exploited for the stabilization of organic residues. The output of the process is usually referred to as biogas. In 2018, biogas and biomethane production was around 35 million tonnes of oil equivalent (Mtoe), with the EU as the leading producer with a capacity of nearly 20 Mtoe.[49] Digestion currently accounts for about 90% of the worldwide biomethane production.[50] However, agricultural crops are strongly localized in the EU, where agricultural crops and crop residues make up almost half of biogas production. This is not true for the US and China, where most of the biogas production comes respectively from municipal solid wastes and from animal manure.[51]
Many varieties of grass, sugar and oily crops, cereals, and corn (including whole plants) are viable for biogas production. An ideal feedstock for digestion should have dry solids content of 20-40%. The process can be operated on wet, pasty biomasses, thus removing the need for extensive drying and lowering the operating costs, but processing of dry biomasses (e.g. grains from cereals) is also possible. As such, the feedstock can be exploited right after harvesting of the plant. Alternatively, it can be stored in silage clamps or baled, which is quite typical for grass feedstocks, with capacity of 10,000 tons of silage for a medium-size plant.[52] Integration with other biofuel production routes (fermentation/FAME) is also possible to increase flexibility.
Although the process occurs naturally, it is usually conducted in controlled conditions, namely in the so-called digesters, to maximize the biomethane yield. Reactor are operated either in the 20-45°C range (mesophilic) or between 50 and 65°C (thermophilic)[53] Mesophilic conditions provide higher stability against load variations or inhibitors, but they also yield lower biogas (and thus biomethane) compared to the thermophilic region.[54] Hence, thermophilic conditions are preferred to mesophilic ones for large-scale centralized units in order to maximize the biogas yield. Depending on the feedstock, biogas in the output varies in the range 50-70% v/v. The remaining share is almost completely made by carbon dioxide. Table 2.4 reports the crop yields and calculated biogas yield for digestion of different crop feedstocks. corn is the preferred choice in the EU due to its high yields.
TABLE 2.4. Biomass productivity (as tons of dry solids per hectare) and methane yield for some relevant feedstocks.[55]
Carbon dioxide makes a large share of the biogas stream and it must be removed to achieve a sufficient biomethane purity (above 95%) to feed it to the grid. Upgrading technologies exploit the different properties of the biogas components to separate them, with water scrubbing and membrane separation accounting for almost 60% of biomethane production globally today.[56] The captured CO2 can either be stored or sold to local industries (i.e. beverages and food, enhanced oil recovery), depending on the local market and logistics. Alternatively, carbon dioxide can be converted to methane, thus raising the overall biomethane yield of the plant. This is possible through methanation, which is a catalyzed reaction conducted at high temperature (300-400°C) in presence of Fe or Ni catalysts. However, great care must be taken in the presence of trace contaminants, which may poison the methanation catalysts. This include ammonia, H2S, and other Sulfur-derived species, which may be found in the biogas stream depending on the feedstock. As a result, further purification of the biogas is required, thus raising the energy and operating costs of the process.
The obtained biomethane can be fed to the natural gas grid or used as a drop-in biofuel for transport. As the technology for anaerobic digestion has been long exploited, its commercial deployment is less critical compared to other technologies. In 2018 the estimated average costs of biogas production in centralized small- (100 m3 h-1), medium- (250 m3 h-1), and large-scale (750 m3 h-1) digesters were respectively about 57 USD/MWh, 44 USD/ MWh and 32 USD/MWh.[57] Clearly, larger capacities result in reduced capital investments and especially reduced operating costs, but the regional context, especially logistics, also plays a relevant role. Indeed, the costs related to handling and transportation of the feedstock may be critical, in particular when the local infrastructure is poor. This will not only result in increased overall costs for the plant, but it will also negatively affect the carbon balance of the process, as trucks or other heavy-duty vehicles will be engaged for the biomass transportation for local retailers to the centralized facility.
2.3 Advanced Biofuels: feedstocks
This section deals with advanced technologies for the conversion of a vast group of 2G and 3G biomass into biofuels. This large ensemble of processes shares the ambition to overcome the main issue of 1G biofuels, that is to say the competition with food. New 2G feedstocks are thus mobilized, based on agri-food residues, lignocellulosic crops and municipal/industrial wastes. Additionally, 3G feedstocks based on algae cultivations have recently attracted attention thanks to their ability to flourish on poor/unsuitable land or water, thus reducing greatly the land usage, and their great flexibility.
2.3.1 Forest and wood-processing residues
This class refers to all raw materials generated from forests management (forestry residues) as well as from the wood-processing industries. Forestry residues are usually left on the ground during management operations. This includes several varieties of grass and fast-growing trees, which are high yield raw materials. The low bulk density of these feedstocks can be a strong constraint for their valorization, as it may raise significantly handling and transportation costs. This can be avoided through the deployment of small facilities next to the collection sites (e.g. skid plant or small digesters), thus cutting transportation costs. Alternatively grinding and palletization is possible to ease handling and transportation of the biomass. Clearly the choice will strongly depend on the local context, namely the availability of infrastructure.
A possible application of forestry residues is the biochemical conversion to ethanol, but the high content of lignin requires dedicated mechanical or chemical pre-treatments. These treatments depend on the type of biomass (i.e. the relative content of lignin) but they significantly contribute to the overall costs of operation. Typically, hardwood species like birch or acacia contain more degradable lignin components compared to softwoods like pine or whitewood. Provided this demanding pre-treatment, the thermochemical treatment of the feedstock (see corresponding section) may be preferable for the economic profitability of the process, also due to its higher flexibility.
Wood-processing waste from the lumber industry and paper processing usually do not require pre-treatment for their handling. As for forestry residues, conversion of lumber and paper industry wastes to ethanol is partially hindered by the recalcitrant nature of the substrate. Again, it may be more attractive to pursue the thermochemical route, to convert such feedstocks to either char, bio-oil or syngas. In particular, pulp black liquor from the paper industry can be effectively subjected to hydrothermal liquefaction (see corresponding section) to produce bio-oil for marine and road applications. Alternatively, it can be gasified to produce synthetic fuels or biogas.
2.3.2 Agricultural residues
Agricultural residues include a wide variety of wastes from agricultural crop harvesting, coming in the form of leaves, seed, pods, straw, and stalks. They are often left on the ground and remain unused due to the high costs of recovery and transportation. In rural areas crop residues are used either as animal feed or fuel for cooking or they can be exploited as natural fertilizer for the fields once burned to ashes.[58]
An example of this is India, where commonly rice straw is either burned or exploited as fuel for brick industry or domestic uses. Open-field burning of crop residues is an easy solution for farmers for clearing the fields from uncollected residues, but it contributes to GHG emissions substantially. It has been estimated that in 2016 the US, Brazil, China, and India altogether burned 181.8 MT of crop wastes (including rice, wheat, corn, and sugarcane residues), resulting in 15.8 MT of CO2 emissions.[59] Moreover, burning of the residues is also negatively affecting the soil health due to destruction of microbes and loss of nutrients. Depending on the type of waste, agricultural residues fit into a wide range of applications. Wet biomasses and many crop residues can be converted to biogas through digestion. Lignocellulosic residues with sufficient sugar and/or starch contents, like corn cobs, may undergo hydrolysis and be subsequently fermented to 2G bioethanol. Oleaginous residues from oil crops can be refined/grounded to obtain vegetable oils, which can be used to produce biodiesel via transesterification and/or HVO through hydrotreating.
The production of crops residues is constantly increasing globally. Cherubin et al. estimated the production of crop residues in four regions (USA, Asia, Africa and Europe) from different crops (cereals, legumes, oilseed, sugar and tubers) in the year 2003 and 2013.[60] Comparing the grand total, world residues increased from 3803 MT in 2003 to 5011 MT in 2013, corresponding to a net increase of 31.7%. Moreover, a study by Hiloidhari et al. estimated that a total dry biomass from 26 different crops in India of 686 MT, of which 34% (234 MT) is not exploited for competing uses (cooking, heating, fertilizer, etc.) and is available as feedstock for bioenergy.[61]
When dealing with agricultural residues, one should always bear in mind that for most processes the raw materials will require pre-treatment before biofuel production. This will in turn affect the biofuel production cost, especially for energy-intensive processes like bioethanol production. Moreover, the generally low bulk density of such feedstocks result in increased handling and transportation costs. This limit is partially overcome through palletization and briquetting, but it may play a crucial role in the profitability of the technology, especially in regions where poor infrastructure is available. Finally, excessive harvesting of the leftovers may negatively affect the soil balance, depending on the considered residues.
2.3.3 Industrial and municipal wastes
A huge variety of wastes can be recovered from industrial processes. Apart from crop residues, the food sector accounts for wastes produced along the entire food processing supply chain. This includes residues from food processing itself, like peel or zests, but also products discarded as they are not meeting quality requirements. Moreover, significant amounts of uneaten food are discarded by restaurants, hotels and private homes without exploitation. It is estimated that roughly one-third of the processed food is lost along the supply chain. This is a huge reservoir of unused biomass, which could be easily exploited for a wide range of applications. For instance, digestion of food residues to produce biogas is possible. Discarded oil seeds, used cooking oil (UCO) and animal fats represents an attractive feedstock for conversion to FAME/HVO. The UCO market for HVO production is expanding rapidly, especially in European countries and in the US, due to the fuel's superior characteristics.
Wastewaters are also generated during vegetables, fruit, and meat washing. These effluents are rich in solid and dispersed organic matter and could be sent directly to digestion to produce biogas. At the same, washing wastewaters might be also mobilized for fermentation to bioethanol if the sugar or starch content is sufficiently high, although high processing costs are expected for the concentration of the product. Moreover, the oil fraction commonly separated during wastewater pre-treatments could again be valorized through transesterification to FAME or hydrotreating to HVO/HEVA.
Municipal wastes come in two main forms. Municipal solid waste (MSW) are generally disposed of in open landfill, where biogas is naturally generated due to decomposition of the wastes. Such gas can be recovered and purified to be fed in the natural gas grid. MSW could be treated in a digester to increase the yield of biomethane during anaerobic decomposition. Also, the organic fraction of MSW can be exploited for the production of bio-oil through hydrothermal liquefaction or synthetic fuels through gasification and chemical conversion of syngas. Another relevant residue from municipality is sewage, which is still eligible for digestion to biogas. The sludge resulting at the end of digestion could be incinerated to produce power -- although increased processing costs are expected for drying e stabilization --, but pyrolysis is also an option to produce even more biogas from the same raw material.
2.3.4 Algae as a new feedstock
With the term algae we refer to a broad group of autotrophic organisms, which can be coarsely divided into "macroalgae", including larger species like kelps, and "microalgae", referring to both smaller species and cyanobacteria, a different prokaryotic species. Algae are conventionally classified as a separate, third generation group of biomasses owing to some specific features. They are not in competition with food as for 2G feedstocks, but they are also characterized by fast growing rate, high lipid content and more accessible carbon source compared to lignocellulosic materials. Most algae typically flourish in aquatic environments, but there are also some terrestrial species, which are still fitting to grow in non-arable lands.
Algae are able to produce biomass using CO2 as a carbon source through photo-biochemical processes. Such conversion is performed at a faster rate compared to terrestrial plants: roughly 2 g of CO2 are required per gram of generated biomass.[62] Lipids stored inside algae are no different from many plant lipids, except for a consistent amount of fatty acid components with higher degrees of unsaturation, and their amount can be increased by putting the algae culture under nutrients (e.g. Nitrogen) stress.[63] Selection of the best strains is a crucial point for the feasibility of the process. As estimated, there are one to ten million microalgal species on the Earth and more than 40,000 species have been identified.[64] The preferred strains will display high lipid content and fast growth rate.
2.4 Advanced Biofuels: technologies
Such feedstocks can be exploited according to three different platforms. The biochemical platform, featuring the conversion of lignocellulosic biomass to ethanol via fermentation. The oleochemical platform, where FOG (fats, oils and grease), microbial oils and algae oils are converted to FAME or HVO/HEFA. Finally, the thermochemical platform entails the conversion of different 2G/3G biomasses to syngas through thermochemical treatments and then to different fuel and chemicals, including methanol, MTBE, synthetic Fischer-Tropsch fuels. In 2018 all these novel technologies accounted only for 9% of biofuel production, corresponding to 13.5 billion L.[65] This limited share is mainly due to the low maturity and poor know-how of most advanced technologies, resulting in increased production costs and high risk for the deployment at the commercial scale. Moreover, the majority of such biofuels (12 billion L) came from hydrotreating of 2G feedstocks to jet-fuel, while lignocellulosic ethanol and thermochemical processes only accounted for 1% of the global biofuel production.[66]
2.4.1 Cellulosic Bioethanol
Many lignocellulosic feedstocks from the agri-food industry can be exploited for advanced fermentation. This includes woody and fast-growth plants, whose main components are lignin, hemicellulose and cellulose. The latter is usually the major component in lignocellulosic biomass and it is the main carbon source for biochemical conversion. However, due to the refractory nature of the feedstock, fermentation of the raw feedstock is not possible, as lignin and lignocellulosic fractions have an inhibitory effect on the yeasts.
As a result, pre-treatment of the biomass is required to make sugars available for conversion. This is recognized as the most crucial step and the main challenge for technology implementation. The complex lignocellulose structure must be break-down to make cellulose and hemicellulose available for the fermentative step and allow lignin removal. Several chemical and mechanical solutions are available, such as dilute acids, ammonia extraction and steam explosion, but there is no consensus on a preferred technology. The removal efficiency can vary widely in the range 30-75%.[67] Moreover, most of these processes are conducted in harsh conditions (high temperature or pressure) and they usually make up for 30-40 % of the total cost of the process.[68] Lignin is broken-down to smaller, soluble fragments, which can be removed. However, care must be taken in the possible production of lignin-derived inhibitors, including some aldehydes, weak organic acids and phenolic compounds, which can hinder the fermentative process.[69]
The biomass is then subjected to enzymatic hydrolysis. This stage is more demanding compared to 1G starchy crops, mainly due to the complexity and variety of hemicellulose structure, and a large ensemble of enzymes is exploited to convert long-chain polymers to simple monomeric sugars, namely glucose from cellulose and hexose/pentose (e.g. xylose) from hemicellulose. The main side-product up to this point is lignin, which can be valorized for polyester production or it could be converted to liquid biofuels through thermochemical processes (see corresponding section). Finally, the biomass is converted to bioethanol. The most common yeasts for ethanol production (i.e. S. Cerevisiae) are not very effective in converting pentose. This may significantly reduce the process yield, as pentose often makes up a large share of the biomass, especially feedstocks rich in hemicellulose. Microbial engineering is a possible way to increase both the yeast ability to degrade pentose and its tolerance to ethanol and lignin. However, such approaches are still far from maturity and further research is required. As for 1G bioethanol, extensive concentration of the product is required through evaporation, distillation, and dehydration. Again, this is the most energy-intensive stage of the process, raising greatly the operating costs and reducing its profitability.
Table 2.5 reports some illustrative figures for biomass productivity and ethanol yield for different 2G feedstocks. Agri-food residues and woody feedstocks display great potential thanks to their relatively high yield. In the case of sugarcane bagasse, a side-product of either sugar industry or 1G ethanol plants, integration with conventional biofuel plants is also possible. In this way, side-products like cellulose could be used for supplying thermal energy for the main conversion. Clearly, this also entails investments for the additional pre-treatment stages and adapting the microbial consortium. Another approach to reduce capital investments for advanced bioethanol is conducting simultaneous saccharification and fermentation (SSF), thus cutting the costs related to the two separate units. Still, the production costs for 2G bioethanol are rather high and cannot compete with conventional fuels. For instance, production costs of lignocellulosic ethanol from softwood in the US were estimated as 0.90 USD/L, almost twice the average costs for US corn or Brazil sugarcane ethanol.
TABLE 2.5. Biomass productivity (as tons of dry solids per hectare per year) and ethanol yield for some relevant 2G feedstocks.[70]
Nonetheless, some industrial solutions for advanced bioethanol production are already available. Cellulosic bioethanol started to be commercialized in January 2013 by Beta Renewables in Crescentino (Italy), producing 40,000 tons of ethanol per year.[71] Other notable application of lignocellulosic ethanol at an industrial scale include DuPont (Nevada, Iowa, USA), Abengoa (Hungton, Kansas, USA), and Poet/DSM (Emmetsburg, Iowa, USA), with capacity in the range 90-113 million liters per year. However, lignocellulosic ethanol is still a risky and demanding market, also considering the fierce competition of cheap gasoline and/or corn ethanol. Both Abeongoa and DuPont plants have been closed and sold - the latter in 2018 to the German company VerBio, to be used for the production of biogas -, while Poet/DSM has been operating at reduced capacity for many years and has reverted to R&D to improve process efficiency. Moreover, these ventures accounted for a minimal share in global biofuel production. In fact, in 2018 lignocellulosic bioethanol and thermochemical processes (see corresponding section) only accounted for 1% of global biofuel production (1.4 billion L).[72]
In addition, some varieties of sugarcane were genetically modified to improve productivity and resilience (energy cane). Such crops display the ability to effectively grow in areas not suited for sugar cane cultivation, thus reducing competition with food and exploiting degraded/unused lands. Examples of energy canes are EunergyCane by Alkol Biotech and Cana Vertix by GranBio[73], which are effectively exploited for cellulosic ethanol production.
2.4.2 Advanced bio-oils
Algae are a rich source of lipids, which can be recovered (typically via hexane extraction) and exploited for transesterification to FAME and/or hydrotreated to drop-in HVO. At the same time, the high content of sugars in the residual biomass makes it viable for conversion to bioethanol. Also, the remaining feedstock can be exploited for anaerobic digestion to biogas.
Thus, algae make a rather versatile feedstock for biofuel production. However, their industrial scalability is currently hampered by the energy demands related to both cultivation and harvesting phases. Farming can be achieved both in open ponds and dedicated bioreactors. Open ponds are attractive because they are cheap and easy to operate, but they require large extensions of land and provide lower productivity. Thus, the application of open ponds should be considered in regions where there is high availability of land and limited or no competition with arable lands.[74] On the other hand, bioreactors can achieve higher cultivation density (e.g. vertical columns layout) and higher productivity, but both capital and operational costs are substantially increased due to the complexity of the configuration.
Moreover, the harvesting and dewatering of the biomass are recognized as the major bottleneck, especially for microalgae systems where they account for 20-30% of the total production costs.[75] Macroalgae harvesting is generally based on mechanical systems with lower requirements.[76] Conversely, microalgae recovery is achieved through different separation processes, including filtration, centrifugation, flotation and electrophoresis.[77] The selection of a specific treatment will depend on the feedstock characteristics, such as strains fragility (centrifugation) or the density range (flotation). Moreover, flotation and flocculation require the addition of flocculants (i.e. ferric and aluminum chlorides), which may pose environmental concerns and limit the use of side-products. A comparative study by Norsker et al. reported that for the most economic cultivation system the biomass production cost was 4.15 €/kg[78], much higher than common feedstocks like soybean, wheat or corn.
Currently, biofuel production from algae requires further optimization before reaching the proper industrial scalability, as the overall capital and operational costs are still relatively high compared to other solutions. Process profitability may be increased through co-production of value-added products (e.g. fertilizers, food additives, cosmetics), which can sustain the main production line, or by exploiting flue gas and wastewaters as source of carbon and nutrients.[79] Still, the production costs of micro algae biodiesel was estimated to be 2-3 times higher than 1G and 2G counterparts, ranging from 1.6-2.2 USD/L for open ponds and around 4.7 USD/L for photobioreactors.[80]
Bio-oils can also be harvested from selected strains of yeasts, which are able to convert the excess carbon in their culture medium to lipids and store in their cells in the form of lipid droplets. This behavior is common to both oleaginous and non-oleaginous yeasts (e.g. S. Cerevisiae), but oleaginous yeasts can store high amounts of lipids (at least 20% by weight) in their cells, while other microbial species are typically limited to a maximum of 10% of their dry weight. The selection of a proper feedstock is relevant, as it strongly influences the final content of the lipid fraction and accounts for most of the process cost, up to 85%.[81]
Most of the sugar industry by-products, such as sugarcane molasses, bagasse and husks are low-cost, viable carbon sources for yeasts growth.[82] Also, lignocellulosic materials can be exploited such as wheat and rice straws or corn stover. After cultivation, the yeasts can be harvested either by settling or centrifugation and the lipid fraction is recovered through hexane extraction. The obtained oils are converted to FAME through transesterification and the resulting biodiesel can be used for blending or further upgraded with hydrotreating.
2.4.3 Biogas from wastes
2G biomasses can be converted to biogas through anaerobic digestion similarly to agricultural crops. A great variety of feedstocks may be exploited, including animal manure, agri-food residues, wastewater sludge, and lignocellulosic crops. In the EU, biogas production is currently dominated by agricultural crops, crop residues and animal manure.[83] The latter is also very relevant in China, where it is the predominant source for household digesters in rural areas (roughly 70% of the total installed capacity in China).[84] Conversely, US biogas comes mainly from municipal solid wastes, with landfill gas collection making up for nearly 90% of US production.[85]
Every feedstock has some inherent drawbacks for the process, such as suboptimal carbon to nitrogen ratio (C/N) or low availability of carbon source. To partially overcome this issue, co-digestion of many raw materials is possible. Lignocellulosic feedstocks are attractive due to their high yield, but their usage is hindered by the need of costly pre-treatments (e.g. dilute acids) as for 2G fermentation. Crop residues and animal manure are the largest sources worldwide and, in many cases, they are nearly zero-cost or even negative if disposal of the waste is required by law. This does not affect the biogas costs dramatically, though, as installing the digesters usually make up for 70-95% of the total costs. Moreover, integration with other biofuel technologies is possible, for instance when exploiting the residual fermentation mash from bioethanol plants. In Table 2.6 the average energy yield in biogas for different types of feedstock are synthetized. They are provided as tons of oil equivalent, corresponding to the energy released by burning one ton of crude (about 42 GJ). For comparison, it is recalled that bioethanol and biodiesel heating values are roughly 27 GJ/ton and 38 GJ/ton respectively - with some variability according to the considered feedstock.
TABLE 2.6. Average biogas yield (as ton of oil equivalent per ton of feedstock type).[86][87]
The biogas yield lies in a wide range. Industrial waste provides the highest yield, but landfill gas is a very low-cost source. Animal manure yield is quite low, but it can be exploited in house-hold digesters with limited capital investments. In fact, landfill gas recovery and basic household digesters average costs were estimated respectively around 8 USD/MWh and 11 USD/MWh. Implementation of digestion in wastewater plants is possible, but high investments are required resulting in average costs of about 50 USD/MWh.[88] According to this general picture, a huge potential for biogas production is available around the world. However, most of the viable feedstocks are currently neglected or utterly underused. In fact, the worldwide biogas production in 2018 was 35 Mtoe, a very small fraction of the estimated overall potential of biogas (570 Mtoe) and biomethane (730 Mtoe).[89] Full utilization of the biogas sustainable potential could cover some roughly 20% of today's worldwide gas demand.[90]
2.4.4 Thermochemical processes
Pyrolysis
Pyrolysis is a thermochemical process featuring the conversion of biomass to solid, liquid and gaseous products at high temperature and in absence of oxygen. The feedstock is progressively reduced to carbonaceous solids (char), liquid bio-oil (tar) and a gaseous mix of mainly hydrogen, CO, carbon dioxide and methane. Pyrolysis can be exploited to make recalcitrant biomasses like lignocellulosic crops and residues viable for gasification. Alternatively, the resulting bio-oil can be upgraded through transesterification to FAME or possibly hydrotreating to HVO, while the gaseous products can be purified and exploited for synthetic fuel production.
The product distribution can be adjusted by properly tuning the operating conditions. Currently, the most common set-up relies on fast pyrolysis, where the biomass is treated in the temperature range of 400-550°C with very short vapor residence times (down to 1-2 s). What makes this option particularly attractive is the possibility to achieve a high yield of bio-oil (up to 75% by weight) compared to other conditions. The obtained bio-oil is a viscous, brownish mixture of oxygenated organics -- including alcohols, esters, phenolic compounds and lignin oligomers -- and thus its oxygen content is rather high (up to 40%).[91] This implies that bio-oil is quite reactive (i.e. not very stable) and requires upgrading through hydrotreating before its application either as biodiesel or as bio-jet. Still, non-negligible amounts of the other phases are produced, calling for side-processes for their valorization. This would be desirable to raise the economic profitability of the main process - according to a biorefinery approach -, but one should also take into account the regional constraints (market demand, logistics).
Provided that fast pyrolysis is an endothermic process and very short residence times are required, very high heating rates are required (up to 1000°C/s), negatively affecting the overall energy balance. Still, it is possible to exploit the biochar for partial or complete oxidation to provide energy to the main process. Alternatively, zeolites can be used to catalyze the reaction. The catalyst allows reducing the operating temperature to less than 500°C and delivering bio-oil with a lower oxygen content. This variation of the process is generally referred to as in-situ catalytic pyrolysis.
To properly operate the process, the feedstock needs to be extensively dried and grounded to fine particles. This adds significant operating costs and may hinder the exploitation of some advanced feedstocks when the pre- treatments are excessively costly. In this respect, intermediate pyrolysis may be a sound alternative, at least to overcome the grounding issue. In fact, this process implies lower heating rate (i.e. higher residence time) in the order of 300 °C/min and it works fine even with coarse particles. These milder conditions imply a lower yield of bio-oil, though, typically around 50% by weight.
To date, some industrial scale facilities performing pyrolysis are already operational. Some relevant examples include Fortum in Joensuu (Finland), Ensyn plants in Ontario (Canada) and BTG in Hengelo (the Netherlands), with capacity ranging from 50 to 300 tons per day roughly. Yearly production is still limited compared to other advanced bioprocesses and most of the generated bio-oil is not employed for drop-in fuel production, but rather as co-feed for refineries and combined heat and power (CHP) or for food flavoring manufacturing.
Hydrothermal Liquefaction (plus HTC, HTG)
Hydrothermal processes imply the treatment of the biomass in presence of hot water in sub-critical, near critical or supercritical conditions. In hydrothermal liquefaction (HTL) the biomass is liquefied at high pressure (50-250 bar) and moderate temperature of 250-550 °C, delivering an oily stream, sometimes referred to as bio-crude.[92]
The greatest advantage of the HTL process is the ability to deliver a single, liquid output. In addition, it is possible to process wet biomass, which removes the costs related to drying and enables the exploitation of a wider variety of feedstocks (wastewaters, manure, and municipal/industrial sludges). HTL yield in bio-oil is lower compared to fast pyrolysis, but the bio-crude is more stable and displays much lower oxygen content compared to pyrolysis oil, usually in the range 5-10%.[93] Nonetheless, upgrading through hydrotreating is still required for drop-in application, especially in the case of bio-jet, but the hydrogen consumption is typically lower. Despite being a very promising technology, little attention has been paid to HTL thus far and only few demonstrations with pilot plants were attempted globally.[94]
Other hydrothermal processes exploit different operating conditions to switch the main output to either solid or gaseous products. Hydrothermal carbonization (HTC) is performed at mild conditions (less than 220 °C and 30 bar) and yields in a solid carbon source, akin to coal. Apart from the application as primary biofuel (i.e. direct burning), the biochar can also be exploited for gasification and conversion to synthetic fuels. By contrast, treatment in supercritical conditions at 600-700 °C allows converting most of the feedstock to mainly hydrogen and carbon dioxide, with or without the addition of catalysts.[95] The production of a gas rich in methane is also possible by varying process conditions and applying proper catalyst.[96]
Gasification (Biomass to Liquid)
In the gasification process the raw materials (solid or liquid) are converted to gases using air/oxygen at high temperature. The output is a mixture of hydrogen, carbon monoxide, CO2, methane, and minor impurities. Such stream is generally referred to as syngas, synthesis gas or producer gas and it can be exploited, after cleaning and conditioning, for the conversion to synthetic fuels (e.g. Fischer-Tropsch fuels). This route for biomass conversion is usually labeled as 'Biomass-to-Liquid' (BtL) processes.
Gasification is suitable for all biomasses coming from the agri-food sector, wood residues, municipal solid or liquid wastes, and aquatic biomasses. According to the reactor configuration, pre-treatment of the feedstock is required to a greater or lesser extent. For instance, biomass feed to entrained flow gasifiers requires raw materials fine grained with a maximum grain size of 1 mm.[97] This is not a great issue when dealing with coal-like materials, but it can become quite a challenge for lignocellulosic feedstocks, increasing the costs significantly. Further increase in the overall process costs may come from difficulty in feedstock handling (e.g. straw) or from high moisture feeds (> 30%), requiring extensive drying prior to gasification.[98] An alternative way to overcome such issues is the use of pyrolysis as a pre-treatment for gasification. In this case, raw biomass is converted to a bio-slurry, which is easier to handle during gasification.
The process is typically carried out at 800-1200 °C and it is endothermic. A stream of air is required for the partial combustion of the biomass, which is accounting for the required energy (autothermal mode). However, this will result in a strongly diluted product, due to the presence of Nitrogen in the air. Alternatively, pure oxygen can be used for the combustion, avoiding the issues related to Nitrogen dilution. In this case, an air separation unit (ASU) will be required to provide the oxygen stream, increasing the overall process costs. Still, the low cost of electricity, which accounts for most of ASU operating costs, make this extra unit generally feasible.
The composition of the output gases is strongly influenced by the operating condition. Apart from the operating temperature, addition of steam to the oxygen stream will favor the water-gas-shift reaction, resulting in an increased generation of hydrogen. This is particularly beneficial when gasification is exploited for Fischer- Tropsch synthesis, as syngas with a high H2/CO ratio is required for the process. Conversely, addition of hydrogen will boost the production of methane, making the output stream viable for biomethane production. Along with the main gaseous products minor amounts of tar and char are produced as well.
In any case, the obtained syngas will require further processing before conversion to synthetic fuels. For instance, the catalysts employed for Fischer-Tropsch synthesis are vulnerable to poisoning from Sulphur and Nitrogen.[99] Regardless of the syngas use, such species should still be removed from the stream to prevent the formation of NOx and SOx during combustion of the synthetic biofuel. Separation of residual tar and char are also required to prevent catalyst deactivation and to meet biofuel specifications. There are several approaches to mitigate the production of char and tar, but they all come at a cost, like addition of steam (worsened energy balance), increase air/biomass ratio (more biomass lost for combustion), or increase the temperature (higher capital and operational costs). If the syngas is destined for catalysis to liquid fuels, the gas cleanup technologies may also separate CO2, which then dominates the byproduct gas stream and is suitable for geologic storage.
For all these reasons, syngas cleaning can be one of the most demanding but also rewarding steps along the Biomass-to-Liquid route.
Even though gasification of biomass is widespread around the globe, it is mainly devoted to the production of energy via co-firing in furnaces or CHP plants rather than production of biofuels for transport. Nonetheless, few commercial facilities are available. Enerkem gasifier in Westbury (Quebec, Canada) convert treated wood, wood residues and municipal solid wastes to syngas for alcohols production (4000 t/y of ethanol). ThermoChem Recovery International has successfully deployed a fully integrated biorefinery (Durham, North Carolina, USA), where organic residues and municipal solid wastes are gasified, and the obtained syngas is converted to Fischer-Tropsch liquid products (1 t/y). Karlsruhe Institute of Technology (KIT) demonstration plant combines pyrolysis pre-treatment, gasification and chemical synthesis to convert straws into DME (608 t/y) and synthetic gasoline fuels (360 t/y).
2.4.5 Synthetic biofuels (Biomass-to-Liquid)
The syngas from gasification can be exploited for a sound variety of synthetic biofuels. Each synthesis has its own requirements in terms of operating conditions (temperature, pressure) and catalyst, but the lower quality of bio-derived syngas is surely a key issue, which is hampering the deployment of BtL platform. Methanation was already mentioned earlier as a possible route for conversion of syngas to methane through a high temperature, catalyzed reaction (see crops digestion to biogas).
In addition, two relevant conversion routes, namely methanol/DME and Fischer-Tropsch synthesis, are presented in the following sections. These are consolidated processes in the chemical and fossil fuels industry, whose chemistry is well-known and industrial-scale infrastructure are available. Thus, when syngas from biomass is fed, little adjustments are expected compared to the conventional conditions of the processes.
Methanol and DME Synthesis
Methanol production is a consolidated technology, based on the exothermic conversion of syngas. It is conducted at 220-280 °C and 50-100 bar in presence of a catalyst based on Copper, Zinc and Aluminum oxides. Hence, syngas must be cleaned from Sulphur and halogens to prevent poisoning of the catalyst. Methanol is the main product of the process, but methane, ethane, ethers, higher alcohols, and DME are also obtained as by-products. Furthermore, the conversion per pass is quite low and recycling of the unreacted syngas is required to achieve high yield. Consequently, distillation of products is conducted to separate methanol from lighter and heavier species, increasing energy costs. A variation of the process, where reaction is operated at 260-525 °C and 30-300 bar, allows producing mixed alcohols, but further research is required to make commercialization feasible.[100]
The obtained methanol is not eligible as a drop-in biofuel, but it can be used for blending in gasoline along with ethanol. Notably, ENI and FCA have launched a new fuel made up of 15% methanol and 5% bio-ethanol.
Commercialized with the brand name "A20", the fuel is reported to provide 3% less CO2 emissions due to its peculiar formulation.[101] Alternatively, it can be converted to dimethyl-ether (DME) and gasoline. This is possible through catalytic dehydration of methanol at 250-300 °C and 15-30 bar in presence of alumina or zeolites catalyst. The reaction is exothermic and water is the main by-product. DME is viable as fuel for heavy-duty transport due to its high cetane number, but it will need compression before end-use being gas at standard conditions. By pushing dehydration further, DME can be converted to gasoline. The process is conducted at 250-300 °C and 30 bar under zeolite catalyst and the output consists of gasoline-range hydrocarbons (44 wt.%) and water (56 wt.%).[102]
Fischer-Tropsch (F-T) Synthesis
Syngas can also be exploited for the production of synthetic liquid fuels through the Fischer-Tropsch (F-T) synthesis. This process involves the conversion of syngas to hydrocarbons and water through catalytic hydrogenation. The reaction is carried out at 200-350 °C and pressure up to 275 bar, it is strongly exothermic and proceeds via the addition of -CH2- building blocks to form short-/long-chain hydrocarbons.
Straight-chain alkanes and alkenes are the main reaction products, but some isomers, methane, alcohols, and other oxygenated products are also obtained in smaller amounts. The product distribution can be adjusted by properly tuning the operating conditions, selecting the most suited catalyst, and adjusting the hydrogen over CO ratio (usually around 2.2-2.5). Iron-based catalysts and higher temperature typically shift the distribution to gasoline-range hydrocarbons and methane, while Cobalt-based catalysts, lower temperature and high pressure are preferred to obtain long-chain hydrocarbons (mainly diesel, but also naphtha cuts).
As some oxygenated products are also formed, a downstream unit for water separation is to be included. Also, lighter products (i.e. LPG) must be separated to allow recycling unreacted syngas. Removal of Sulphur, Nitrogen and tar from the syngas is fundamental to preserve the catalyst, while adjustment of the H2/CO is necessary to obtain the desired product distribution. The latter may not be required in the presence of Iron- based catalysts due to their activity towards water-gas-shift reaction. The synthetic liquids obtained from F-T synthesis require upgrading through hydrotreating to meet specifications as drop-in biofuels or can be blended with fossil cuts.
The great advantage of Fischer-Tropsch synthesis compared to other processes is certainly the possibility to tune the product distribution depending on regional market needs. Moreover, little adjustment is expected when switching to biomass feed, except for feed purification against poisoning. Table 2.7 summarizes some techno-economic assessment of biofuel production through gasification and F-T synthesis. The liquid fuel cost varies widely depending on the feedstock, but it could be competitive with fossil fuels depending on the considered region. This is especially true for low cost feedstocks like switchgrass and woody biomasses.
TABLE 2.7. Production capacity (as barrel per day) and liquid fuel production cost for gasification and F-T synthesis of some relevant 2G feedstocks. (Switchgrass[103], Residual Woodstraw[104], Corn stover[105], Woody Biomass[106][107])
2.5 Perspectives
2.5.1 Overview of biofuels technologies
The biochemical platform comprises the conversion of sugar-containing crops to ethanol and the production of biogas through anaerobic digestion. Regarding fermentation, the process is well-established, but the low concentration of obtained ethanol is the choke point. The purification of bioethanol is costly and energy-intensive and significant investments are required for the realization of new, dedicated infrastructures. Moreover, the pre-treatment of recalcitrant feedstocks (i.e. lignocellulosic biomasses) further increases the overall costs of the process, making it less attractive than the biomass-to-liquid route. As a result, gasification of the biomass, especially for 2G, may be more convenient compared to its hydrolysis for ethanol production.
As for biogas production, digestion is a mature technology, but it is susceptible to biomass characteristics and requires significant pre-treatment, especially for some advanced feedstocks. Co-feeding of different biomasses may mitigate this issue, while centralized, large-scale plants are preferred to optimize the process and reduce operating costs. However, this may not be feasible when the logistics is poor, increasing excessively handling and transportation costs. Furthermore, separation of CO2 and impurities is required to meet biomethane quality standards. Thus, significant investments are required to provide basic infrastructures for biomass handling, pre-treating and integration in the natural gas grid.
The oleochemical platform comprises both FAME and HVO/HEFA production. The FAME process is well-known, but the poor quality of the obtained biodiesel (requiring extensive upgrading) as well as the susceptibility to biomass variations make it less attractive than hydrotreating. Indeed, FAME profitability at commercial scale is still dubious, also bearing in mind that huge amounts of glycerin are obtained, whose valorization is not always straightforward. Conversely, HVO was successfully scaled-up to industrial level and provides high quality biofuel, which is also eligible for jet-fuel application. This is particularly relevant as electrification of the aviation segment is not yet attainable, thus making HVO the only practicable route for decarbonization of the sector. Moreover, repurposing existing infrastructure and/or co-feeding is possible, cutting the capital investments and the risks connected to technology deployment.
The thermochemical production of biofuels passes through the conversion to syngas. This solution is undoubtedly advantageous in terms of product flexibility, as syngas is eligible for conversion to either gasoline, diesel, methanol or even methane under proper catalyst and operating conditions. Moreover, syngas with H2/CO ratio close to 3 can also be exploited for ammonia production. Many different biomasses are reduced to the same intermediate (i.e. syngas) and then the most fitting conversion route can be selected, depending on the regional context. Furthermore, small capital investments are required compared to other technologies, as repurposing of existing infrastructure is possible for both gasification and syngas conversion. This is the main reason making biomass-to-liquid more convenient for lignocellulosic feedstocks -- especially the most recalcitrant or low-density ones -- compared to a less maturity technology like 2G fermentation to ethanol.
The overall picture clearly shows that biofuels can be a more or less valuable asset depending on many variables, notably the regional context. There is no global optimum in terms of technology profitability, but many local optima according to the local needs and feedstock availability. Framing Table A tries to summarize the key elements for all technologies.
FRAMING TABLE A. Key features of traditional and advanced biofuel technologies.
2.5.2 Competition/synergy with alternative platforms
A sound and wide-ranging assessment of biofuel technologies profitability should take into account other platforms relevant for transport. This includes both electrification of transport segments and use of hydrogen as a fuel.
Electrification appears as the most promising route for substantial reduction of transport GHG emissions on the long term, with a greater potential growth in urban areas. In 2019 sales of electric cars topped 2.1 million globally, surpassing 2018, and raising electric car share to 2.6% of global car sales and 1% of global car stocks.[108] This is the result of a strong policy effort in recent years to push electric car sales and use. However, substantial increase of the current grid is required. Indeed, most of the charging is currently done at home and works with slow chargers. In 2019 chargers reached about 7.3 million worldwide, but 6.5 million of them were private, light-duty vehicle slow chargers in homes, multi-dwelling buildings and workplaces.[109] Instead, public, accessible chargers only accounted for 12% of global light-duty vehicle chargers.[110] Expansion of the grid will be relevant for sustaining the electric car market, electrification of heavy-duty segment and highways.
Such intervention may require huge effort and time, leaving room for biofuels in the meantime. In fact, when no major change in the infrastructure is required, biofuels may act synergistically to foster the shift to full electrification. They could be seen, in this respect, as an intermediate platform before the electric grid is able to step in. Moreover, the high infrastructure costs related to electrification may reduce its profitability compared to some biofuel technologies. This is particularly true for methane, for which the infrastructure is fully available, and for developing, rural areas, where the effort required for deploying the grid is still too high. Finally, electrification of the aviation sector is still critical. Despite the rapid increases in battery energy densities in the past decade, battery chemistries would enable at most all-electric fly distances of around 1000 km, covering only about 20% of jet-fuel demand.[111] This implies that HVO/HEFA are still the only viable solution to achieve decarbonization of the aviation segment. The technology for hydrotreating is mature and the repurposing of existing infrastructure is possible, thus making HVO as the most attractive solution for replacing fossil jet-fuel.
Hydrogen is also gaining increasing attention as an alternative source of "clean energy" both in the public debate and for private and public investments. Hydrogen reacts in presence of oxygen to form water, releasing energy, without any CO2 emission. It should be stressed, though, that when reaction is achieved with air NOx are also produced. It has been successfully employed as an energy source in fuel cell vehicles (FCV), typically passenger car, and in fuel cell buses. The global FCV stock nearly doubled to 25,210 units at the end of 2019 (12,350 new vehicles), more than doubling the 5,800 purchased in 2018.[112] Traditionally, hydrogen is obtained from fossil sources, namely steam reforming of methane or coal gasification, which are still the dominant feedstock.
Biomass gasification could be an alternative way for H2 production, but the low content of hydrogen in biomasses (usually below 10%) is a very strong constraint. Electrolysis of water is also possible when a proper water source is available. Indeed, the projects and the installed electrolyzer capacity have increased from less than 1 MW in 2010 to more than 25 MW in 2019.[113]
However, the major constraints on hydrogen exploitation lies in the storage and utilization rather than the manufacturing process. Since the volumetric energy density of hydrogen is low, storage under compression is required and tank volume is large compared to conventional fuels. This clearly pose many issues to safety, as hydrogen is very reactive, flammable and it tends to leak easily. Moreover, hydrogen is very aggressive with conventional construction materials, including high-strength low-alloy steel, inducing the so-called hydrogen embrittlement. As a result, existing infrastructure cannot be exploited for pure hydrogen transport. The methane grid, for instance, could only carry mixture with low hydrogen fraction.
Accordingly, biofuels can be seen not just in competition with hydrogen and especially electricity, but mainly as a synergistic resource. They could be seen as a sort of battery, allowing easy and reliable storage of energy for when the need comes. For instance, biofuels could be exploited for modulating electricity consumption during peak demands. Moreover, this approach is a fortiori suitable for inherently intermittent sources of energy like wind or solar power. Framing Table B synthesizes the main advantages/disadvantages of biofuel technologies compared to electricity and hydrogen.
FRAMING TABLE B. Main pros and cons for traditional/advanced biofuel technologies compared to electricity and hydrogen platforms.
P.S. Nigam, A. Singh / Progress in Energy and Combustion Science 37 (2011) 52-68 ↩︎
IEA. (2019). Transport biofuels. In Renewables 2019: Analysis and forecast to 2024. ↩︎
International Energy Agency. (2020). Transport biofuels. In Renewables 2020: Analysis and forecast to 2025. ↩︎
Ibid. ↩︎
Ibid. ↩︎
Tian, Y., Zhao, L., Meng, H., Sun, L., Yan, J. 2009. Estimation of un-used land potential for biofuels development in (the) People's Republic of China. Applied Energy 86: 77--85. doi: 10.1016/j.apenergy.2009.06.007. ↩︎
S.C. de Vries, G.W.J. van de Ven, M.K. van Ittersum, K.E. Giller, Resource use efficiency and environmental performance of nine major biofuel crops, processed by first-generation conversion techniques, Biomass and Bioenergy 34 (2010) 588--601. [https://doi.org/10.1016/j.biombioe.2010.01.001]. ↩︎
B.E. Della-Bianca, T.O. Basso, B.U. Stambuk, L.C. Basso, A.K. Gombert, What do we know about the yeast strains from the Brazilian fuel ethanol industry?, Appl. Microbiol. Biotechnol. 97 (2013) 979--991. [https://doi.org/10.1007/s00253-012-4631-x]. ↩︎
F. Mueller-Langer, S. Majer, A. Perimenis, Biofuels: A Technical, Economic and Environmental Comparison, in: L.Y. Bronicki (Ed.), Renewable energy systems, Springer, New York, 2012, pp. 110--137. ↩︎
Ibid. ↩︎
FAO, The state of food and agriculture 2008: Prospects, risks and opportunities, Food and Agriculture Organization of the United Nations, Rome, 2008. ↩︎
Ibid. ↩︎
E. Close, A. Gnansounou, A. Dauriat, Ethanol fuel from biomass: a review, J Sci Ind Res, 64 (2005), pp. 809-821 ↩︎
A. Bonomi, O. Cavallet, M.P. Cunha, M.A.P. da, Lima, Virtual biorefinery: an optimization strategy for renewable carbon valorization (1st ed), Springer (2015) ↩︎
Renewable Fuels Association (RFA). Pocket guide to ethanol. Washington; 2015 ↩︎
FAO, The state of food and agriculture 2008: Prospects, risks and opportunities, Food and Agriculture Organization of the United Nations, Rome, 2008. ↩︎
M. Balat, H. Balat, C. Öz, Progress in bioethanol processing, Progress in Energy and Combustion Science 34 (2008) 551--573. [https://doi.org/10.1016/]j. pecs.2007.11.001. ↩︎
UNICA. Números finais da safra 2014/2015 e iniciais da nova safra 2015/2016. União Da Indústria Cana-de-Açúcar; 2016. Accessed July 2020. ↩︎
Agricultural Marketing Resource Center. An Overview of the Biodiesel Market: Production, Imports, Feedstocks and Profitability. [https://www.agmrc.org/] [renewable-energy/renewable-energy-climate-change-report/Renewable-energy-climate-change-report/march-2016-report/an-overview-of-the-biodiesel-] [market-production-imports-feedstocks-and-profitability]. Accessed May 2020. ↩︎
International Energy Agency. (2020). Transport biofuels. In Renewables 2020: Analysis and forecast to 2025. ↩︎
Ibid. ↩︎
FAOSTAT, FAO Statistics Division: [http://www.fao.org/faostat/en/#home. Accessed November 2020]. ↩︎
W.M.J. Achten, L. Verchot, Y.J. Franken, E. Mathijs, V.P. Singh, R. Aerts, B. Muys, Jatropha bio-diesel production and use, Biomass and Bioenergy 32 (2008) 1063--1084. [https://doi.org/10.1016/j.biombioe.2008.03.003]. ↩︎
A.E. Atabani, A.S. Silitonga, I.A. Badruddin, T.M.I. Mahlia, H.H. Masjuki, S. Mekhilef, A comprehensive review on biodiesel as an alternative energy resource and its characteristics, Renewable and Sustainable Energy Reviews 16 (2012) 2070--2093. [https://doi.org/10.1016/j.rser.2012.01.003]. ↩︎
M. Athar, S. Zaidi, A review of the feedstocks, catalysts, and intensification techniques for sustainable biodiesel production, Journal of Environmental Chemical Engineering 8 (2020) 104523. [https://doi.org/10.1016/j.jece.2020.104523]; S. Dey, N.M. Reang, P.K. Das, M. Deb, A comprehensive study on prospects of economy, environment, and efficiency of palm oil biodiesel as a renewable fuel, Journal of Cleaner Production (2020) 124981. [https://doi.org/10.1016/j.jclepro.2020.124981]. ↩︎
A.E. Atabani, A.S. Silitonga, I.A. Badruddin, T.M.I. Mahlia, H.H. Masjuki, S. Mekhilef, A comprehensive review on biodiesel as an alternative energy resource and its characteristics, Renewable and Sustainable Energy Reviews 16 (2012) 2070--2093. [https://doi.org/10.1016/j.rser.2012.01.003]. ↩︎
M. Athar, S. Zaidi, A review of the feedstocks, catalysts, and intensification techniques for sustainable biodiesel production, Journal of Environmental Chemical Engineering 8 (2020) 104523. [https://doi.org/10.1016/j.jece.2020.104523]. ↩︎
M.J. Ramos, C.M. Fernández, A. Casas, L. Rodríguez, A. Pérez, Influence of fatty acid composition of raw materials on biodiesel properties, Bioresour. Technol. 100 (2009) 261--268. [https://doi.org/10.1016/j.biortech.2008.06.039]. ↩︎
A.E. Atabani, A.S. Silitonga, I.A. Badruddin, T.M.I. Mahlia, H.H. Masjuki, S. Mekhilef, A comprehensive review on biodiesel as an alternative energy resource and its characteristics, Renewable and Sustainable Energy Reviews 16 (2012) 2070--2093. [https://doi.org/10.1016/j.rser.2012.01.003]. ↩︎
M. Athar, S. Zaidi, A review of the feedstocks, catalysts, and intensification techniques for sustainable biodiesel production, Journal of Environmental Chemical Engineering 8 (2020) 104523. [https://doi.org/10.1016/j.jece.2020.104523]. ↩︎
M.J. Ramos, C.M. Fernández, A. Casas, L. Rodríguez, A. Pérez, Influence of fatty acid composition of raw materials on biodiesel properties, Bioresour. Technol. 100 (2009) 261--268. [https://doi.org/10.1016/j.biortech.2008.06.039]. ↩︎
A.E. Atabani, et al., A comprehensive review on biodiesel. ↩︎
M. Athar, S. Zaidi, A review of the feedstocks. ↩︎
M.J. Ramos, et al., Influence of fatty acid composition. ↩︎
A.E. Atabani, et al., A comprehensive review on biodiesel. ↩︎
IEA (2019), How competitive is biofuel production in Brazil and the United States?. [https://www.iea.org/articles/how-competitive-is-biofuel-production-in-] [brazil-and-the-united-states]. Accessed November 2020. ↩︎
Ibid. ↩︎
M. Johnston, T. Holloway, A global comparison of national biodiesel production potentials, Environ. Sci. Technol. 41 (2007) 7967--7973. [https://doi.org/10.1021/] [es062459k]. ↩︎
Yanowitz, Janet, and Robert L. McCormick. 2009. Effect of biodiesel blends on North American heavy-duty diesel engine emissions. European Journal of Lipid Science and Technology 111 (8): 763--772. doi: 10.1002/ejlt.200800245. ↩︎
C.J. Chuck (Ed.), Biofuels for aviation: Feedstocks, technology and implementation, Academic Press is an imprint of Elsevier, Amsterdam, 2016. ↩︎
M.C. Vásquez, E.E. Silva, E.F. Castillo, Hydrotreatment of vegetable oils: A review of the technologies and its developments for jet biofuel production, Biomass and Bioenergy 105 (2017) 197--206. ↩︎
S.-Y. No, Application of hydrotreated vegetable oil from triglyceride based biomass to CI engines -- A review, Fuel 115 (2014) 88--96. [https://doi.org/10.1016/j]. [fuel.2013.07.001]. ↩︎
ENI. Ecofining. [https://www.eni.com/it-IT/attivita/biocarburanti-sostenibili-ecofining-tm.htm]l. Accessed 5 July 2020. ↩︎
Total SA. La Mède: a facility for the energies of tomorrow. [https://www.total.com/energy-expertise/projects/bioenergies/la-mede-a-forward-looking-facility]. Accessed 5 July 2020.; Marathon Petroleum Corporation. Dickinson Refinery. [https://www.marathonpetroleum.com/Operations/Refining/Dickinson-Refinery/]. Accessed 5 July 2020. ↩︎
IEA Bioenergy Task 39, "The potential and challenges of drop-in biofuels: The key role that co-processing will play in its production". ↩︎
International Energy Agency. (2019). Transport biofuels. In Renewables 2019: Analysis and forecast to 2024. ↩︎
M.C. Vásquez, E.E. Silva, E.F. Castillo, Hydrotreatment of vegetable oils: A review of the technologies and its developments for jet biofuel production, Biomass and Bioenergy 105 (2017) 197--206. ↩︎
K. Sunde, A. Brekke, B. Solberg, Environmental Impacts and Costs of Hydrotreated Vegetable Oils, Transesterified Lipids and Woody BTL---A Review, Energies 4 (2011) 845--877. [https://doi.org/10.3390/en4060845]. ↩︎
IEA 2020, "Outlook for biogas and biomethane: prospects for organic growth". ↩︎
Ibid. ↩︎
Ibid. ↩︎
IEA 2011, Technology for anaerobic digestion of crops in Bioenergy Task 37 :Biogas from crop digestion. ↩︎
Kothari, Richa, A. K. Pandey, S. Kumar, V. V. Tyagi, and S. K. Tyagi. 2014. Different aspects of dry anaerobic digestion for bio-energy: An overview. Renewable and Sustainable Energy Reviews 39:174--195. doi: 10.1016/j.rser.2014.07.011. ↩︎
Gupta, Priyanka, Raj Shekhar Singh, Ashish Sachan, Ambarish S. Vidyarthi, and Asha Gupta. 2012. A re-appraisal on intensification of biogas production. Renewable and Sustainable Energy Reviews 16 (7): 4908--4916. doi: 10.1016/j.rser.2012.05.005. ↩︎
IEA 2011, Significance and potential of crop digestion in Bioenergy Task 37: Biogas from crop digestion. ↩︎
Cedigaz (2019). Global biomethane market: Green gas goes global (press release, 20 March). [https://www.cedigaz.org/global-biomethane-market-green-gas-] [goes-global/]. ↩︎
IEA 2020, "Outlook for biogas and biomethane: prospects for organic growth". ↩︎
Prasad, S., Mahesh K. Malav, S. Kumar, Anoop Singh, Deepak Pant, and S. Radhakrishnan. 2018. Enhancement of bio-ethanol production potential of wheat straw by reducing furfural and 5-hydroxymethylfurfural (HMF). Bioresource Technology Reports 4:50--56. doi: 10.1016/j.biteb.2018.09.007. ↩︎
Deshavath, Narendra Naik, Venkata Dasu Veeranki, and Vaibhav V. Goud. 2019. Lignocellulosic feedstocks for the production of bioethanol: availability, structure, and composition. In Sustainable bioenergy: Advances and impacts, ed. Mahendra Rai and Avinash P. Ingle, 1--19. Amsterdam, Netherlands, Cambridge, MA: Elsevier. ↩︎
Cherubin, Maurício Roberto, Dener Márcio da Silva Oliveira, Brigitte Josefine Feigl, Laisa Gouveia Pimentel, Izaias Pinheiro Lisboa, Maria Regina Gmach, Letícia Leal Varanda, Maristela Calvente Morais, Lucas Santos Satiro, Gustavo Vicentini Popin, Sílvia Rodrigues de Paiva, Arthur Klebson Belarmino dos Santos, Ana Luisa Soares de Vasconcelos, Paul Lineker Amaral de Melo, Carlos Eduardo Pellegrino Cerri, and Carlos Clemente Cerri. 2018. Crop residue harvest for bioenergy production and its implications on soil functioning and plant growth: A review. Scientia Agricola 75 (3): 255--272. doi: 10.1590/1678-992X-2016-0459. ↩︎
Hiloidhari, Moonmoon, Dhiman Das, and D. C. Baruah. 2014. Bioenergy potential from crop residue biomass in India. Renewable and Sustainable Energy Reviews 32:504--512. doi: 10.1016/j.rser.2014.01.025. ↩︎
Pienkos, Philip T., and Al Darzins. 2009. The promise and challenges of microalgal-derived biofuels. Biofuels, Bioproducts and Biorefining 3 (4): 431--440. doi: 10.1002/bbb.159. ↩︎
Hu, Qiang, Milton Sommerfeld, Eric Jarvis, Maria Ghirardi, Matthew Posewitz, Michael Seibert, and Al Darzins. 2008. Microalgal triacylglycerols as feedstocks for biofuel production: perspectives and advances. The Plant journal : for cell and molecular biology 54 (4): 621--639. doi: 10.1111/j.1365-313X.2008.03492.x. ↩︎
Wang, Bei. 2010. Microalgae for biofuel production and CO2 sequestration. Hauppauge N.Y.: Nova Science Publishers. ↩︎
International Energy Agency. (2019). Transport biofuels. In Renewables 2019: Analysis and forecast to 2024. ↩︎
Ibid. ↩︎
S. Vieira, M.V. Barros, A.C.N. Sydney, C.M. Piekarski, A.C. de Francisco, L.P.d.S. Vandenberghe, E.B. Sydney, Sustainability of sugarcane lignocellulosic biomass pretreatment for the production of bioethanol, Bioresour. Technol. 299 (2020) 122635. [https://doi.org/10.1016/j.biortech.2019.122635]. ↩︎
Soetaert, Wim, and Erick J. Vandamme. Ü2009. Biofuels. Hoboken, N.J: Wiley. ↩︎
E. Palmqvist, B. Hahn-Hägerdal, Fermentation of lignocellulosic hydrolysates. II: inhibitors and mechanisms of inhibition, Bioresour. Technol. 74 (2000) 25--33. [https://doi.org/10.1016/S0960-8524(99)00161-3]. ↩︎
C. Somerville, H. Youngs, C. Taylor, S.C. Davis, S.P. Long, Feedstocks for lignocellulosic biofuels, Science 329 (2010) 790--792. [https://doi.org/10.1126/] [science.1189268]. ↩︎
Balan, Venkatesh, David Chiaramonti, and Sandeep Kumar. 2013. Review of US and EU initiatives toward development, demonstration, and commercialization of lignocellulosic biofuels. Biofuels, Bioproducts and Biorefining 7 (6): 732--759. doi: 10.1002/bbb.1436. ↩︎
IEA. (2019). Transport biofuels. In Renewables 2019: Analysis and forecast to 2024. ↩︎
GranBio, "What is energy cane?". [http://www.granbio.com.br/en/conteudos/energy-cane]. Accessed October 2020. ↩︎
Singh, Jasvinder, and Sai Gu. 2010. Commercialization potential of microalgae for biofuels production. Renewable and Sustainable Energy Reviews 14 (9): 2596--2610. doi: 10.1016/j.rser.2010.06.014. ↩︎
Uduman, Nyomi, Ying Qi, Michael K. Danquah, Gareth M. Forde, and Andrew Hoadley. 2010. Dewatering of microalgal cultures: A major bottleneck to algae- based fuels. Journal of Renewable and Sustainable Energy 2 (1): 12701. doi: 10.1063/1.3294480. ↩︎
Roesijadi, G., S. B. Jones, L. J. Snowden-Swan and Y. Zhu. 2010. Macroalgae as a biomass feedstock: a preliminary analysis. Pacific Northwest National Laboratory. ↩︎
Uduman N, Qi Y, Danquah MK, Forde GM, Hoadley A. 2010. Dewatering of microalgal cultures: a major bottleneck to algae-based fuels. J Renew Sustain Energy 2:012701. ↩︎
N.-H. Norsker, M.J. Barbosa, M.H. Vermuë, R.H. Wijffels, Microalgal production--a close look at the economics, Biotechnol. Adv. 29 (2011) 24--27. [https://doi]. [org/10.1016/j.biotechadv.2010.08.005]. ↩︎
Peng, Licheng, Christopher Q. Lan, Zisheng Zhang, Cody Sarch, and Matt Laporte. 2015. Control of protozoa contamination and lipid accumulation in Neochloris oleoabundans culture: Effects of pH and dissolved inorganic carbon. Bioresource technology 197:143--151. doi: 10.1016/j.biortech.2015.07.101. ↩︎
R. Davis, A. Aden, P.T. Pienkos, Techno-economic analysis of autotrophic microalgae for fuel production, Applied Energy 88 (2011) 3524--3531. [https://doi]. [org/10.1016/j.apenergy.2011.04.018].; J. Hoffman, R.C. Pate, T. Drennen, J.C. Quinn, Techno-economic assessment of open microalgae production systems, Algal Research 23 (2017) 51--57. [https://doi.org/10.1016/j.algal.2017.01.005]. ↩︎
Leiva-Candia, D. E., S. Pinzi, M. D. Redel-Macías, Apostolis Koutinas, Colin Webb, and M. P. Dorado. 2014. The potential for agro-industrial waste utilization using oleaginous yeast for the production of biodiesel. Fuel 123:33--42. doi: 10.1016/j.fuel.2014.01.054. ↩︎
Freitas, Cláudia, Teresa Margarida Parreira, José Roseiro, Alberto Reis, and Teresa Lopes da Silva. 2014. Selecting low-cost carbon sources for carotenoid and lipid production by the pink yeast Rhodosporidium toruloides NCYC 921 using flow cytometry. Bioresource technology 158:355--359. doi: 10.1016/j.biortech.2014.02.071.; Yousuf, Abu. 2012. Biodiesel from lignocellulosic biomass--prospects and challenges. Waste management (New York, N.Y.) 32 (11): 2061--2067. doi: 10.1016/j. wasman.2012.03.008. ↩︎
IEA 2020, "Outlook for biogas and biomethane: prospects for organic growth". ↩︎
Ibid. ↩︎
Ibid. ↩︎
Ibid. ↩︎
"Food and green" represents food and garden waste (e.g. leaves and grass) disposed of as MSW. ↩︎
Ibid. ↩︎
Ibid. ↩︎
Ibid. ↩︎
Bridgwater, A. V. 2012. Review of fast pyrolysis of biomass and product upgrading. Biomass and Bioenergy 38:68--94. doi: 10.1016/j.biombioe.2011.01.048. ↩︎
Akhtar, Javaid, and Nor Aishah Saidina Amin. 2011. A review on process conditions for optimum bio-oil yield in hydrothermal liquefaction of biomass. Renewable and Sustainable Energy Reviews 15 (3): 1615--1624. doi: 10.1016/j.rser.2010.11.054. ↩︎
Elliott, Douglas C., Patrick Biller, Andrew B. Ross, Andrew J. Schmidt, and Susanne B. Jones. 2015. Hydrothermal liquefaction of biomass: developments from batch to continuous process. Bioresource technology 178:147--156. doi: 10.1016/j.biortech.2014.09.132. ↩︎
Gollakota, A.R.K., Nanda Kishore, and Sai Gu. 2018. A review on hydrothermal liquefaction of biomass. Renewable and Sustainable Energy Reviews 81:1378--1392. doi: 10.1016/j.rser.2017.05.178. ↩︎
Chakinala, Anand G., Derk W. F. Brilman, Wim P.M. van Swaaij, and Sascha R. A. Kersten. 2010. Catalytic and Non-catalytic Supercritical Water Gasification of Microalgae and Glycerol. Industrial & Engineering Chemistry Research 49 (3): 1113--1122. doi: 10.1021/ie9008293. ↩︎
Stucki, Samuel, Frédéric Vogel, Christian Ludwig, Anca G. Haiduc, and Martin Brandenberger. 2009. Catalytic gasification of algae in supercritical water for biofuel production and carbon capture. Energy & Environmental Science 2 (5): 535. doi: 10.1039/b819874h. ↩︎
A. van der Drift, H. Boerrigter, B. Coda, M.K. Cieplik, K. Hemmes, Entrained flow gasification of biomass---Ash behaviour, feeding issues, and system analyses. Report ECN-C--04-039, 2004. ↩︎
Brammer, J. 2002. The influence of feedstock drying on the performance and economics of a biomass gasifier--engine CHP system. Biomass and Bioenergy 22 (4): 271--281. doi: 10.1016/S0961-9534(02)00003-X.; Cummer, K. 2002. Ancillary equipment for biomass gasification. Biomass and Bioenergy 23 (2): 113--128. doi: 10.1016/ S0961-9534(02)00038-7. ↩︎
Dayton, David C., Brian Turk, and Raghubir Gupta. 2019. Syngas Cleanup, Conditioning, and Utilization. In Thermochemical processing of biomass: Conversion into fuels, chemicals and power, ed. Robert C Brown and Robert C. Brown, 125--174. Hoboken, NJ: Wiley. ↩︎
Fang, Kegong, Debao Li, Minggui Lin, Minglin Xiang, Wei Wei, and Yuhan Sun. 2009. A short review of heterogeneous catalytic process for mixed alcohols synthesis via syngas. Catalysis Today 147 (2): 133--138. doi: 10.1016/j.cattod.2009.01.038. ↩︎
"Eni And FCA Have Developed A20, A New Fuel That Pairs Emissions Reduction With Energy Efficiency". 2021. Eni.Com. [https://www.eni.com/en-IT/media/] [press-release/2019/04/eni-and-fca-have-developed-a20-a-new-fuel-that-pairs-emissions-reduction-with-energy-efficiency.htm]l. ↩︎
S.D. Phillips, J.K. Tarud, M.J. Biddy, A. Dutta, Gasoline from Wood via Integrated Gasification, Synthesis, and Methanol-to-Gasoline Technologies, Report NREL TP-5100-47594, 2011. ↩︎
E.D. Larson, H. Jin, F.E. Celik, Large-scale gasification-based coproduction of fuels and electricity from switchgrass, Biofuels, Bioprod. Bioref 3 (2009) 174--194. [https://doi.org/10.1002/bbb.137]. ↩︎
F. Trippe, M. Fröhling, F. Schultmann, R. Stahl, E. Henrich, A. Dalai, Comprehensive techno-economic assessment of dimethyl ether (DME) synthesis and Fischer--Tropsch synthesis as alternative process steps within biomass-to-liquid production, Fuel Processing Technology 106 (2013) 577--586. [https://doi]. [org/10.1016/j.fuproc.2012.09.029]. ↩︎
H. Boerrigter, Economy of Biomass-to-Liquids (BTL) plants.: An engineering assessment, 2006. Available at [http://www.ecn.nl/docs/library/report/2006/] [c06019.pdf] from the Energy research Centre of the Netherlands ([http://www.ecn.nl/]), Postbus 1, 1755 ZG Petten (NL). Accessed November 2020. ↩︎
L. Tock, M. Gassner, F. Maréchal, Thermochemical production of liquid fuels from biomass: Thermo-economic modeling, process design and process integration analysis, Biomass and Bioenergy 34 (2010) 1838--1854. [https://doi.org/10.1016/j.biombioe.2010.07.018]. ↩︎
M. Shahabuddin, M.T. Alam, B.B. Krishna, T. Bhaskar, G. Perkins, A review on the production of renewable aviation fuels from the gasification of biomass and residual wastes, Bioresour. Technol. 312 (2020) 123596. [https://doi.org/10.1016/j.biortech.2020.123596]. ↩︎
IEA 2020, "Global EV Outlook: entering the decade of electric drive?". ↩︎
Ibid. ↩︎
Ibid. ↩︎
Ibid. ↩︎
IEA (2020), Hydrogen, IEA, Paris [https://www.iea.org/reports/hydrogen]. Accessed November 2020 ↩︎
Ibid. ↩︎